Lamination is a great way to protect your packaging from scratches and scuffs. It is a coating that is usually layers of plastic that improves the overall appearance and prevents cracks in the artwork of the packaging. When laminating cardboard, the plastic is bound to the cardboard and though it is great for all the reasons above, there are currently no commercially viable ways to entirely recycle laminated packaging.
Professor Ruoxi (Rachel) Ma, a Graphic Communication instructor at the California Polytechnic State University in San Luis Obispo, stated that laminated packaging is difficult to recycle because it is essentially multiple layers of different types of plastic as well as aluminum that cannot be separated. These plastics have different properties and if mixed together, compromise their quality. Aluminum is recycled differently than plastics and can contaminate a batch of recycled plastics if recycled together.
Ma mentioned that most laminated packaging is not recycled and is burned for landfills due to its money and time-saving aspects.
Plastic Aluminum Laminate Recycling
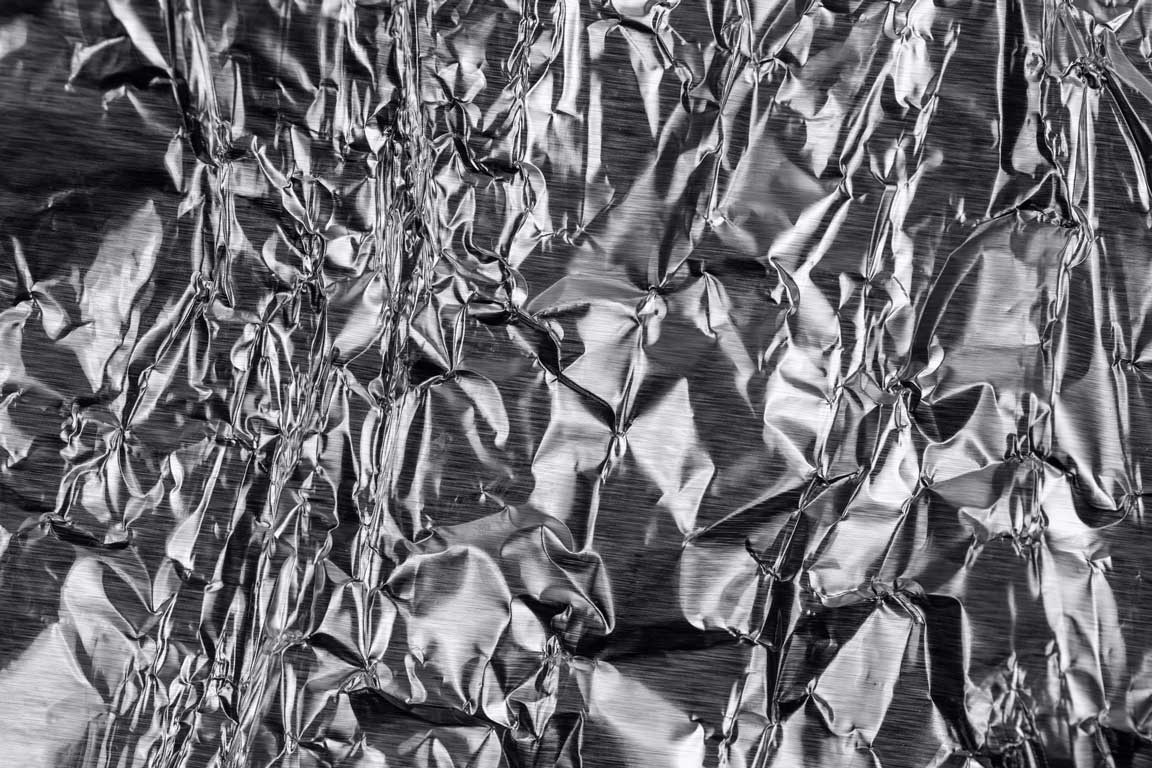
Though laminated packaging is not completely recyclable now, there are some creative and innovative ideas in the works that give insights to the future of laminated packaging!
Enval Limited, a company in the United Kingdom that developed a way to recycle the aluminum in laminated packaging. Their method is called Microwave-Induced Pyrolysis. The process involved starts with mixing shredded laminated waste with carbon, which is a highly microwave-absorbent material. The energy from microwaves is transferred to the waste by thermal conduction from the carbon. It is an energy efficient mechanism and recovers 100% of aluminum in the laminate. The aluminium is clean and ready to recycle. The plastics are degraded and used to make oils and gases for steam and electricity generation, or used in other processes.
Substitutes of Petroleum-Based Lamination
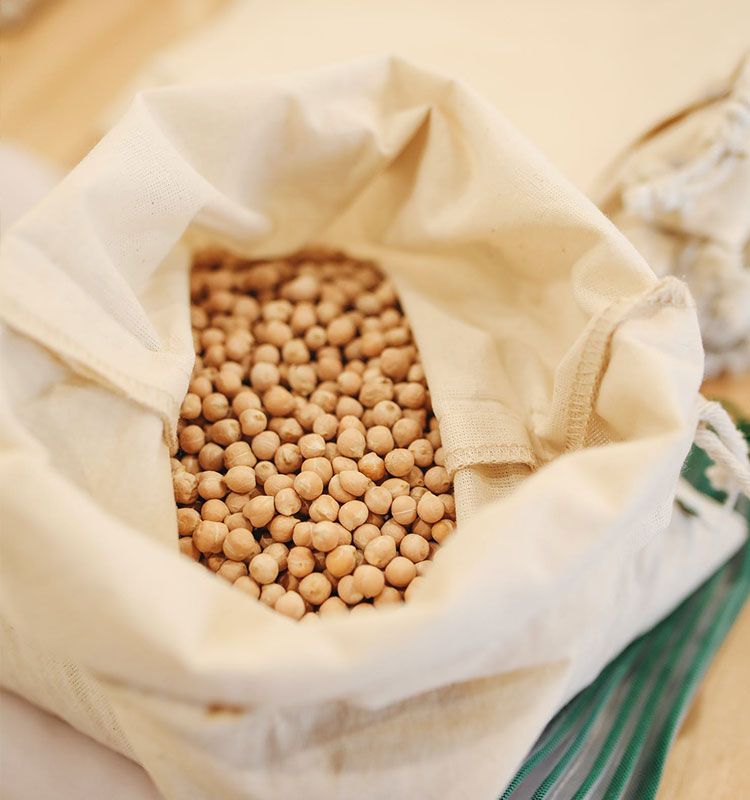
Professor Ma expressed that though there are not many competitive substitutes of petroleum-based lamination, there are some that will be more feasible in the future. Materials such as corn, wood, and other biomass are environmentally friendly due to their shorter decomposition times. They are not practical yet application-wise and cost more than petroleum-based lamination.
A more eco-friendly option that can be implemented now are laminates made by soy polymers. Soy protein laminates are biodegradable and break down faster in landfills than traditional laminates but are not recyclable.
These substitutes are something to think about in looking for more environmentally friendly options for lamination.
Innovation in Lamination
Lamination that can be Recycled with PE Films
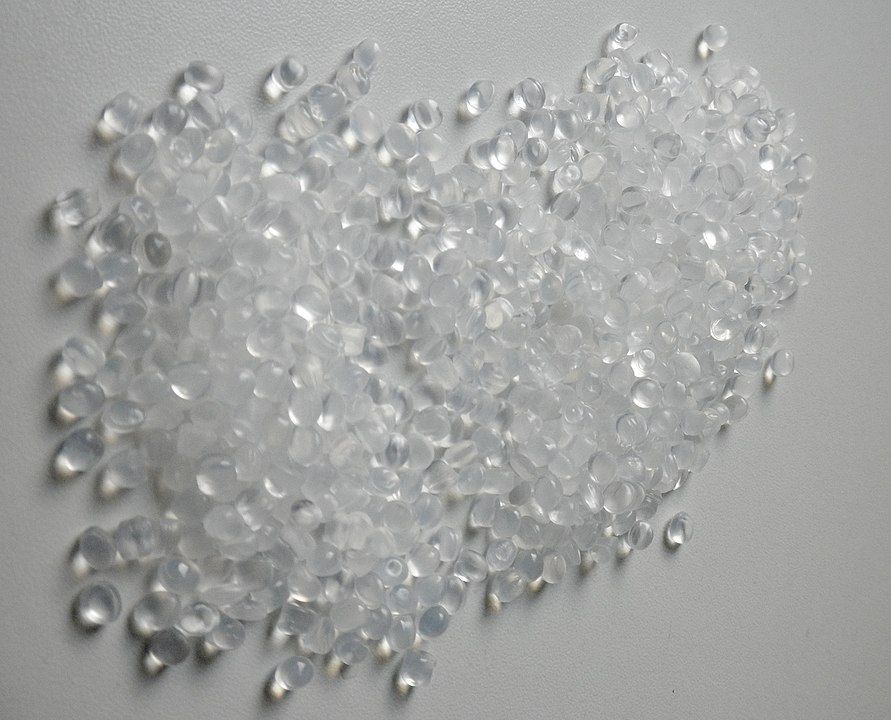
Many companies are currently developing new resins and laminated films with an aim to recycle them with PE films that can be recycled into LDPE plastic products. Some claim to have developed a single layer laminate made from different grades of PE plastic that has both moisture and gas properties. Since it is technically just all one type of plastic, it is more possible to mechanically recycle this type of laminate.
Water Soluble Materials
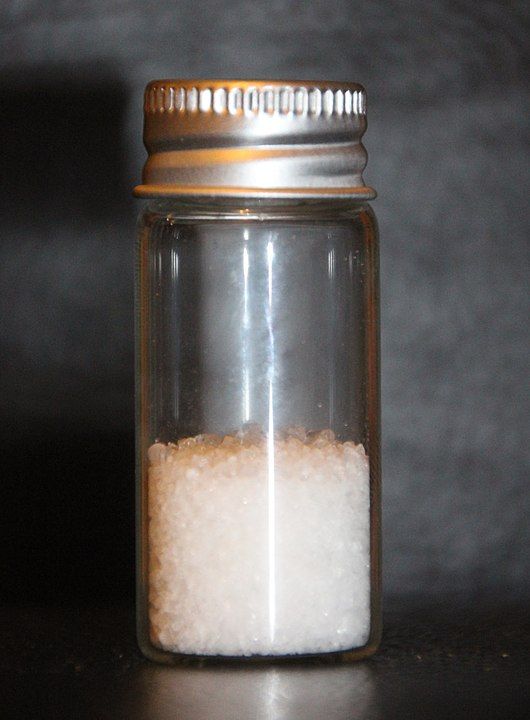
Currently, there are some water soluble barrier materials such as PVOH (polyvinyl alcohol) used on lamination as a gas barrier, though it is more expensive than other barrier materials. These barriers do not replace the actual plastic lamination. They are very limited and some things to consider in using this are compatibility of the recycling process with PE, and other materials have to also be water-soluble.
Paper-Laminates
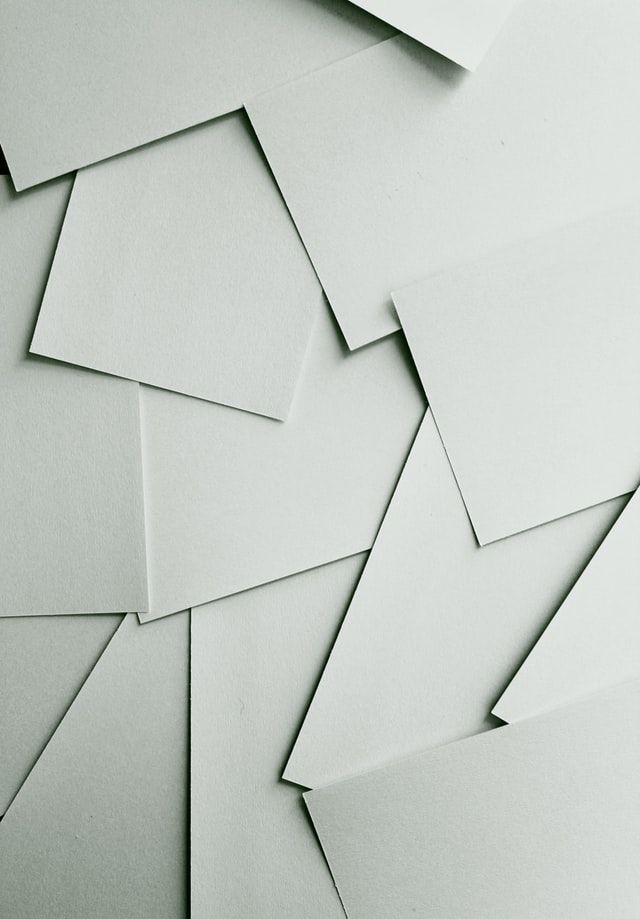
There has been a rise of paper-laminates use with waste processors being able to accept and recycle this type of laminate. They would be recycled through a beverage carton facility rather than a paper mill. Paper-laminates would be sorted out with beverage cartons. The paper would be reused and the rejected ones would be used as fuel for kilns. Logistically, it would need to be worked out with local governments first.
These creative and rising ideas show that there is an ever growing and adapting future for lamination in packaging.
Check out our other blog posts!