Have you ever left boxes under the sun for weeks and notice that it's discolored? Or have you ever seen how your paper or cardboard can get flimsy when it comes into contact with moisture? I'm sure everybody has been in the situation where they receive a cardboard box that’s been in the rain or is soaking wet and barely holding together.
The reality is that paper and cardboard boxes are easily impacted and affected by different weather conditions. These impacts aren’t exclusive to the rain, but can also have effects in heat and humidity. When cardboard comes in contact with any hospitable environment which allows for moisture and bacteria growth, there tends to be damage to both the physical structure and glue holding the cardboard together. This naturally impacts how your packaging materials can look, feel, as well as how strong it remains on a structural level.
This post will focus on how paper and cardboard packaging are affected by the changes that occur in high humidity, cold and dry environments as well as direct exposure to sunlight.
How Humidity Affects Cardboard
High humidity levels lead to internal moisture within cardboard, and this has a direct impact on the strength of corrugated boxes such as mailer boxes or shipping cartons.
Why does this happen? Since wood fibers are used in the creation of cardboard boxes, the natural porosity of wood to absorb moisture when conducting transpiration is maintained even after the entire chemical treating and production of cardboard. This makes cardboard naturally able to absorb moisture at a high level.
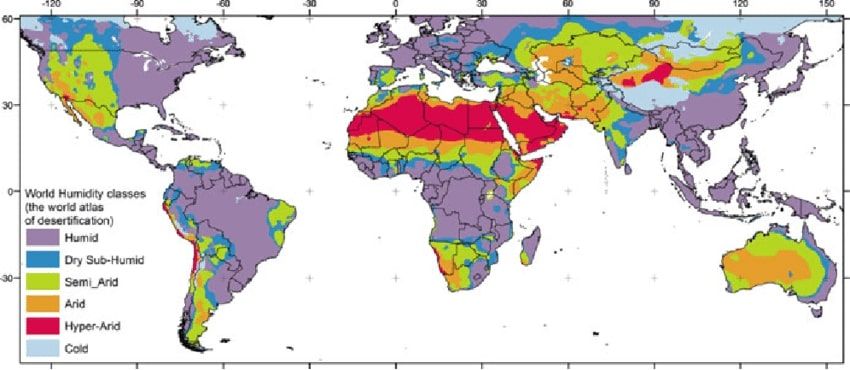
From the map above, humidity levels are highest in areas close to warmer bodies of water. Regions such as China, Southeast Asia, and Eastern USA are such areas with high humidity rates, among others. This signifies a higher moisture content in the air, impacting the structure of cardboard more. With high moisture content within cardboard, not only is the structural integrity compromised but the ability to dry paints and inks is decreased as it increases viscosity when in contact with the moisture.
Humidity is important when considering packaging due to concepts such as relative humidity (RH) and stacking strength. Relative humidity differs from regular humidity as it is the amount of moisture in the air relative to how much is naturally in the air. With 50% RH, the stacking strength of cardboard drops to 80% of its original. This makes summer time the most difficult to maintain packaging and deliveries, as the humidity is the highest at this time. Usually, the solution most people use to counter this moisture is placing desiccant bags inside boxes to remove the moisture.
Packaging Production in High Humidity
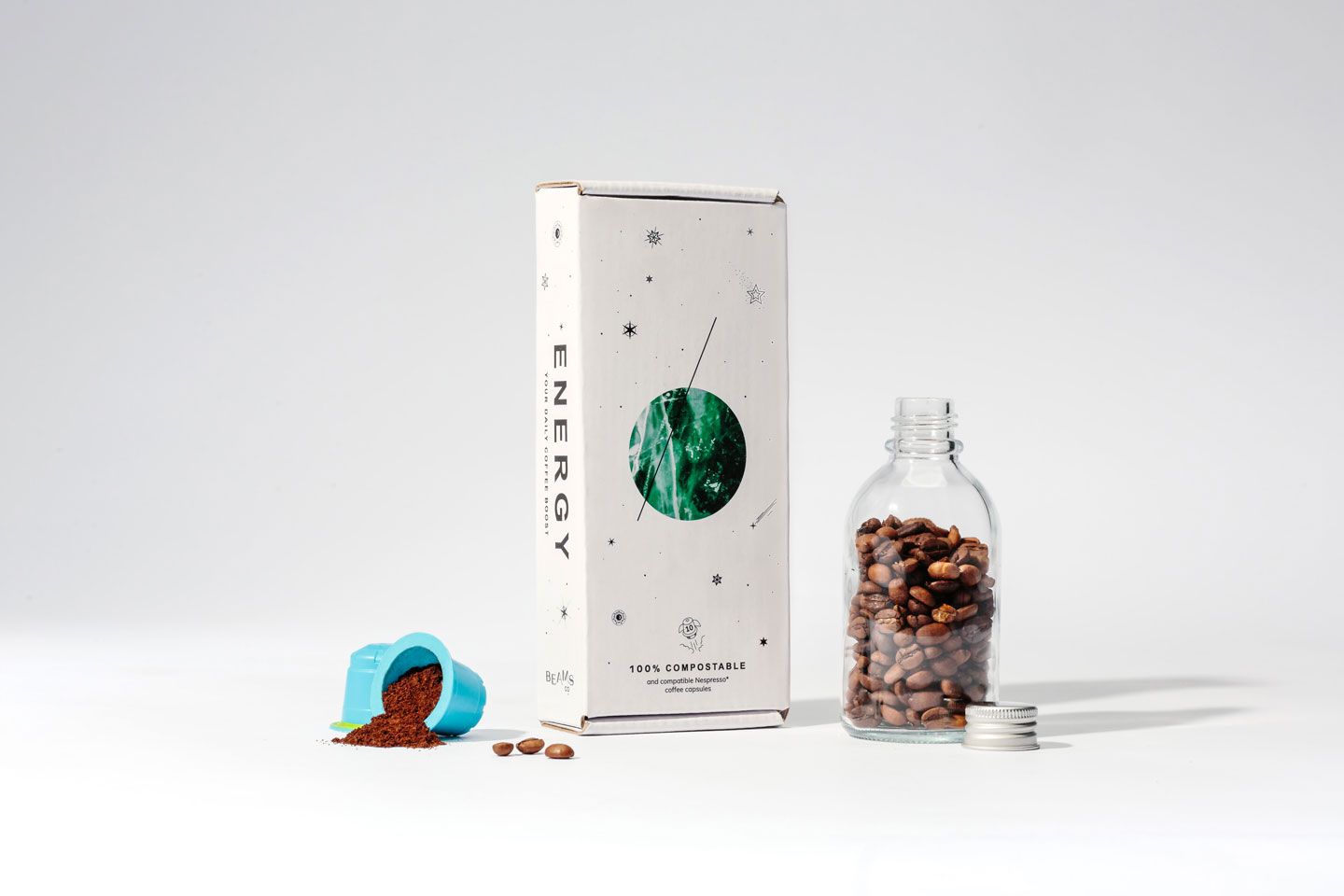
During the production process for corrugated mailer boxes, there's moisture from:
- Ink that's printed
- Glue from laminating a substrate to the corrugated board
- Finishes (such as an aqueous varnish or lamination)
When humidity and moisture levels are high, this means that more time needs to be allocated to drying corrugated boxes. By rushing this process, either the glue or ink may not fully dry, which can cause the cardboard material to appear flimsier, similar to how a sponge retains water and moisture.
If you are ordering packaging from a supplier during the time of year when humidity levels are higher, be sure to account for an additional few days in the production time to allow for your boxes to properly dry.
How Cool and Dry Weather Affects Cardboard
The next case to be aware of is how cardboard reacts in cool and dry weather, opposite to that of hot and humid weather. Generally, as the temperature increases, cardboard loses its compression and its strength. On the other hand, the main concern with cardboard in dryer, colder climates is that the material itself is more brittle and susceptible to cracks and tears in the paper or cardboard.
When cardboard is stored in extremely dry conditions for a prolonged period of time, the extreme lack of moisture makes the cardboard act similarly to a sponge that has had all the water removed. It becomes extremely rigid and brittle, meaning it would be harder to fold a box together without the risk of the paper tearing or cracking.
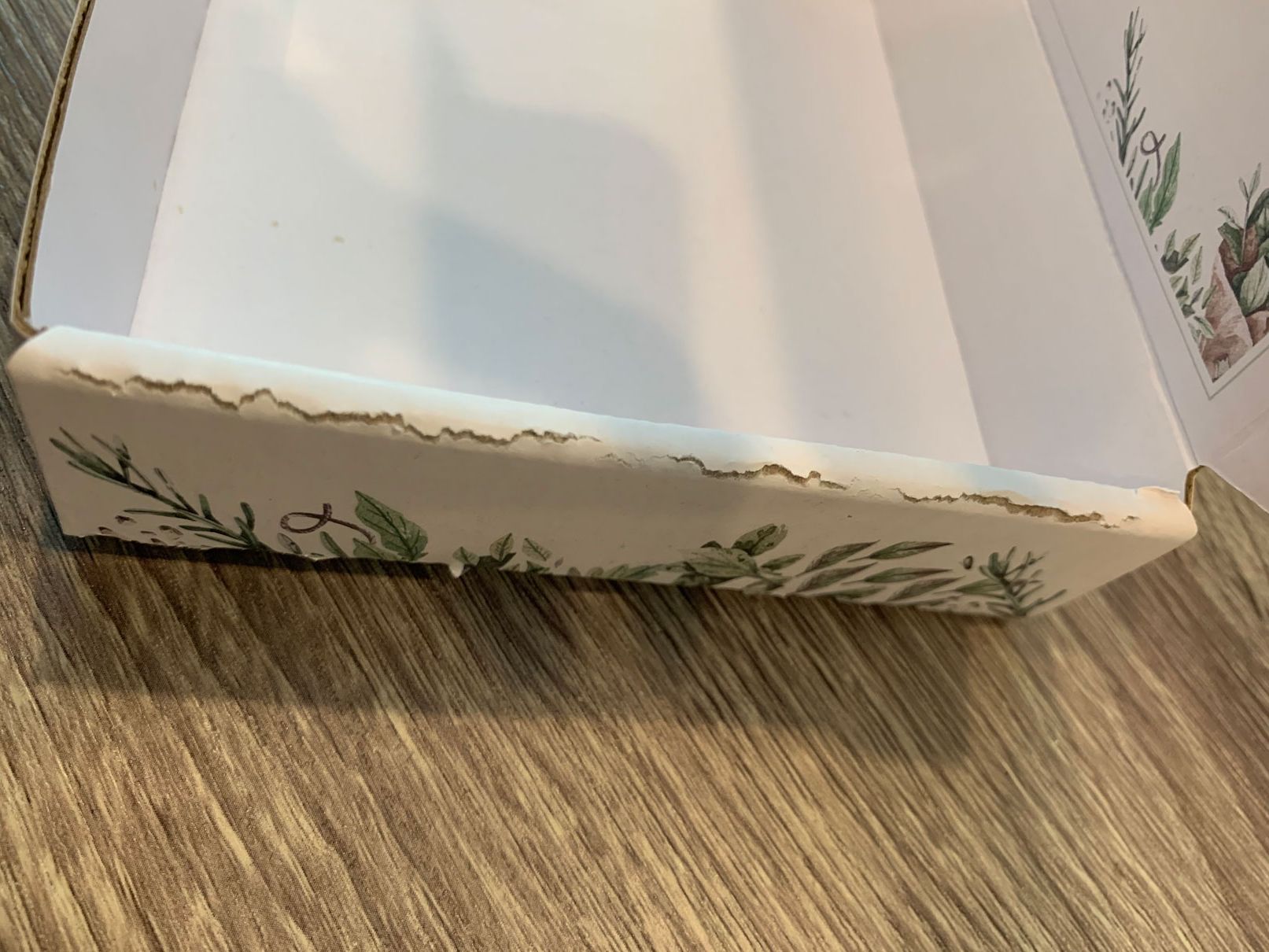
For example, when folding a corrugated mailer box, the crease lines along the folds could lead to cracks on the cardboard due to the very dry piece of cardboard. Cracks would be more visible with printed mailer boxes if they're produced with offset printers, since they consist of substrate layer on top of the cardboard.
To further reduce the likelihood of tears and cracks, especially in dry climates, opt for a lamination finish instead of an aqueous varnish finish. Lamination is comprised of a thin layer of plastic and helps protect the cardboard much more as it acts as a seal. If you're concerned about eco-friendliness, opt for biodegradable lamination!
Ultimately, if you live in dry areas, the best solution would be to use lamination as a means to prevent any chance of tears or cracks in your printed packaging as it acts as a protective barrier between the original box and the moisture or dryness.
How Direct Sunlight Affects Cardboard and Packaging

Generally speaking, having packaging exposed to direct sunlight impacts mainly the internal temperature of the box as well as the colors that could be printed. In both cases, consistent exposure to sunlight can lead to damage to the physical structure of the box as well as the fading of colors. This is known as photodegradation, and is less so the sunlight but the ultraviolet light present within the sunlight. Some dyes and hues are more prone to photodegradation, especially those that are organic. The dilemma is that in this day and age, organic hues and a sustainable process is more environmentally friendly, but the downside is that having all-natural inks and dyes allows for easier photodegradation.
We use soy based ink for all of our packaging, and while it does take slightly longer to dry, the biggest benefit of soy based ink is that it has a lesser tendency to photodegrade compared to other biodegradable inks. This is better for both manufacturer and customer, as it has a lower chance of ruining the ink printer, and is also easily removed to allow for reprinting.
Conclusion
Simply put, packaging needs to be stored in optimal conditions for it to be the most useful in any situation it is used in. Here are a few tips to keep in mind when storing cardboard and other packaging boxes.
- In humid conditions, take your packaging boxes out of its original shipping carton and lay them out flat to let them dry quicker. You can put them under a fan or in an air conditioned room. Ideally, store your boxes in a cool place.
- In cool and dry areas, consider using lamination as a finish. It reduces the chance of moisture damage as well as cracks and creases due to dryness. You could also 'mist' your boxes with a spray to keep them slightly moist when folding them.
- Keep your packaging out of direct sunlight to prevent discoloring caused by photodegradation. Direct sunlight also dries up your packaging and can make them more brittle.
--
About PackMojo
PackMojo makes it easy for businesses to get premium custom packaging at affordable rates. Explore our wide range of packaging solutions or start with a sample kit today!