When it comes to packaging design, aesthetics are important in making a great first impression of your products to your customers. However, it's not just about whether you have a beautiful design or not. The quality of your packaging - including structural integrity, sturdiness, and durability - are all important factors in the practicality of packaging. After all, when you ship your products out to customers, your package will likely go through the diverse (and harsh) conditions of shipping before it reaches your customer.
With that being said, there are different tests you can conduct on your packaging boxes to measure the quality of your packaging. In this post, we'll cover 6 different types of packaging tests that you or your supplier can conduct, along with best practices for each.
1 - Packaging Drop Tests
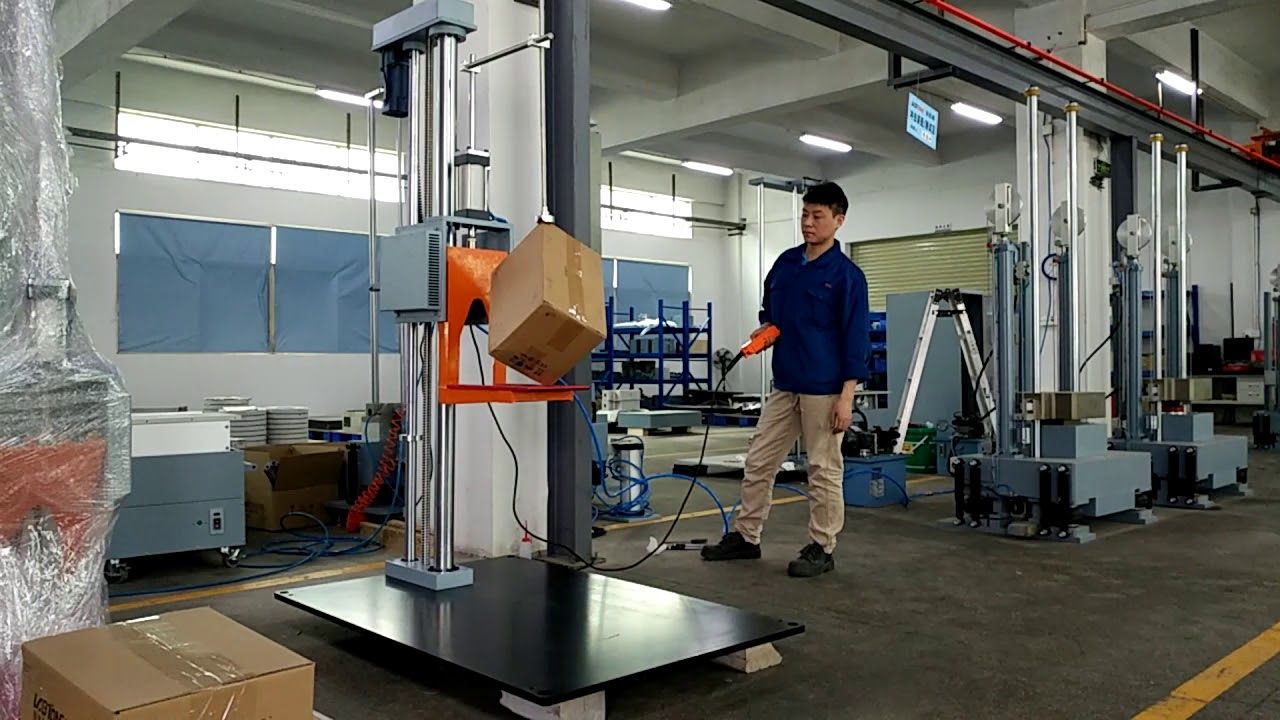
Drop tests drop your packaging at different orientations and heights multiple times to see how your products and packaging hold up in these conditions. The international standard is from ISTA (International Safe Transit Association), with the ISTA 1A drop test procedure being the accepted international standard for drop tests.
When it comes to conducting drop tests, the height at which your shipping carton should be dropped from depends on the weight of the carton itself. These are the appropriate heights at which your carton should be dropped from:
Carton Weight | Drop Height |
---|---|
1-9kg (1-20lb) | 76cm (30") |
10-18kg (21-40lb) | 61cm (24") |
19-27kg (41-60lb) | 46cm (18") |
28-45kg (60-100lb) | 30cm (12") |
46-68kg (101-150lb) | 20cm (8") |
As you can see, lighter cartons are dropped from a higher height than heavier cartons. At any height above 76cm or 30", it becomes unrealistic to run a drop test to see if your packaging will protect your product.
There are a few standards you can follow depending on the organization or carrier for your shipments:
- ISTA: Procedure 3A: Parcel Delivery System Shipments 150 lbs (70kg) or Less (UPS follows this standard)
- ASTM: D7386-16 Standard Practice for Performance Testing of Packages for Single Parcel Delivery System 150 lbs or less
- FedEx: ISTA-6-FedEx-A: Tests for Packaged Products Weighing up to 150 lbs.
The Process
Drop your shipping carton at an appropriate height 10 times from different sides. Here's an example from FedEx:
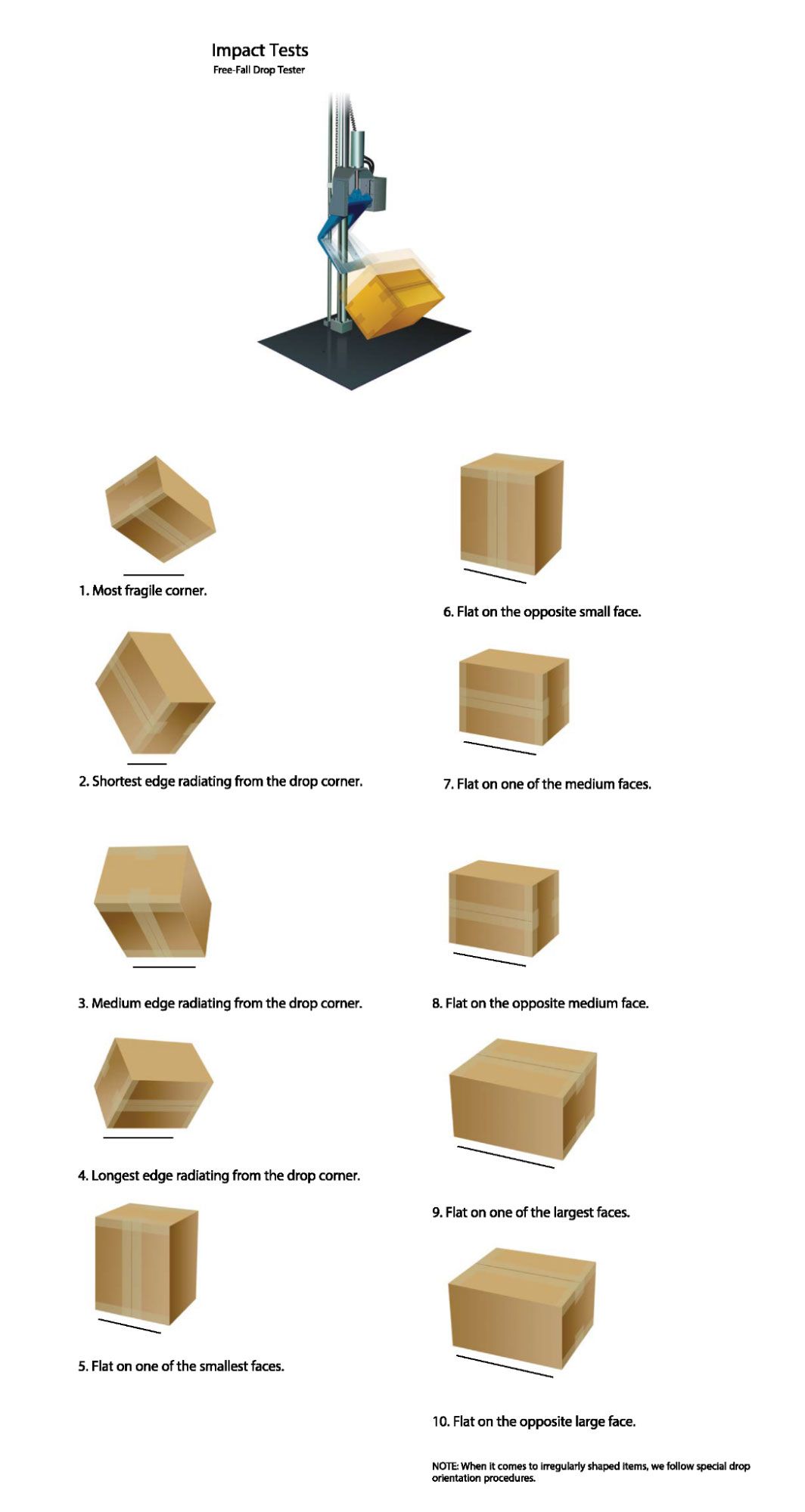
Effectively, you want to be dropping your shipping carton:
- On the most fragile corner (i.e. where it's taped shut)
- On the edges that come from the fragile corner (i.e. 3 drops)
- On the remaining 6 sides
Your carton fails the drop test if any of the following occurs:
- There's significant damage to the shipping carton (it's completely smashed, torn, or is open)
- There's significant damage to the inner packaging box (it's completely smashed, is completely torn or broken)
- The product inside the inner packaging box is deformed, scratched, dented, or damaged and unable to be used
If you see some dents on the corners or edges of your shipping carton after the drop test, that's normal. The purpose of the shipping carton is to protect what's inside, so any deformation to the shipping carton itself is fine as long as the products inside are completely protected completely secure and unharmed from the drop tests.
2 - Edge Crush Test (ECT)
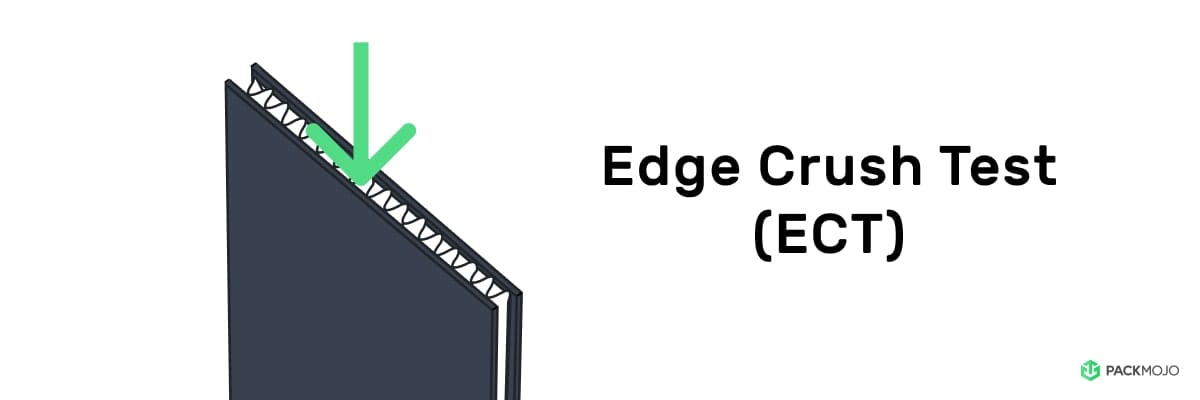
The Edge Crush Test, or ECT, measures how much force the corners and edges of a corrugated material can take until it's crushed. This is important because the corners and edges are mostly responsible for keeping the shipping carton upright and must be strong enough to hold all of the weight (e.g. stacks of cartons) on top of it.
A piece of your corrugated material is inserted upright between the machine and compressed at different pressures. ECT is measured in pounds per inch and is reported as an ECT rating. An ECT rating of 32 is most commonly used as a baseline for single-wall corrugated boxes, and are suitable for most light to medium weight products. A corrugated box with an ECT rating of 32 means that it can withstand a stack of up to 65 pounds.
FedEx and UPS follow ISTA standards for packaging 30 pounds or less to be at least 32 ECT.
3 - Burst Test (Mullen Burst Test)
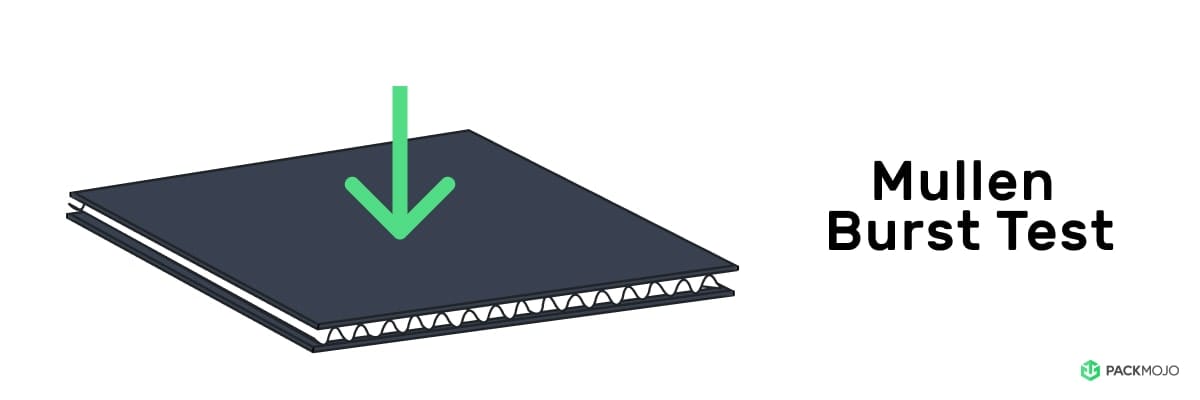
The Mullen Test measures how much force is required to burst the main the force required to burst the corrugated board or paperboard. This is important because it tells you how much force your box can withstand and how much weight your box can hold when your boxes are tossed around, which will likely happen with couriers and their rough handling of packages.
A small piece of your corrugated packaging is inserted flat in between a machine where a small rubber ball applies pressure under the packaging to see how much force it can withstand before bursting. Burst tests are measured in pounds per square inch and are reported as a box rating. For example, a 200# rating means that the box can withstand 200 pounds per square inch force applied before bursting.
So which test is better? That depends on the use case.
- If you're concerned about stacking strength of your cartons, especially if you'll be shipping your packages in pallets, ECT is a better measure.
- If you're concerned about how your shipping carton will fair during the rough conditions of shipping, the Mullen Test is a better measure.
Here are equivalency charts for these two tests, but remember that they are not completely identical as they are two different tests:
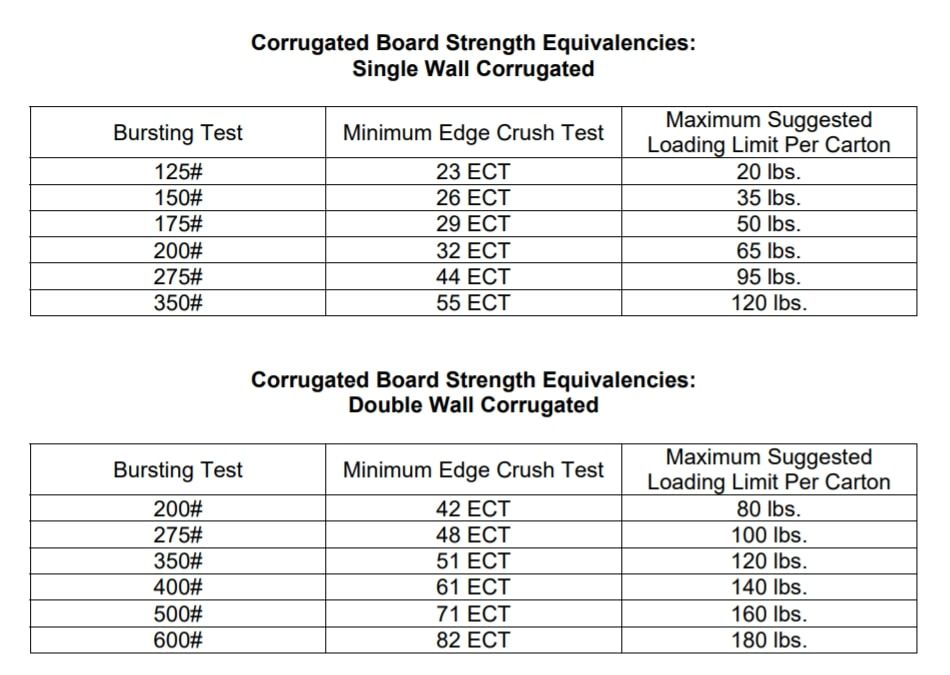
4 - Packaging Vibration Test
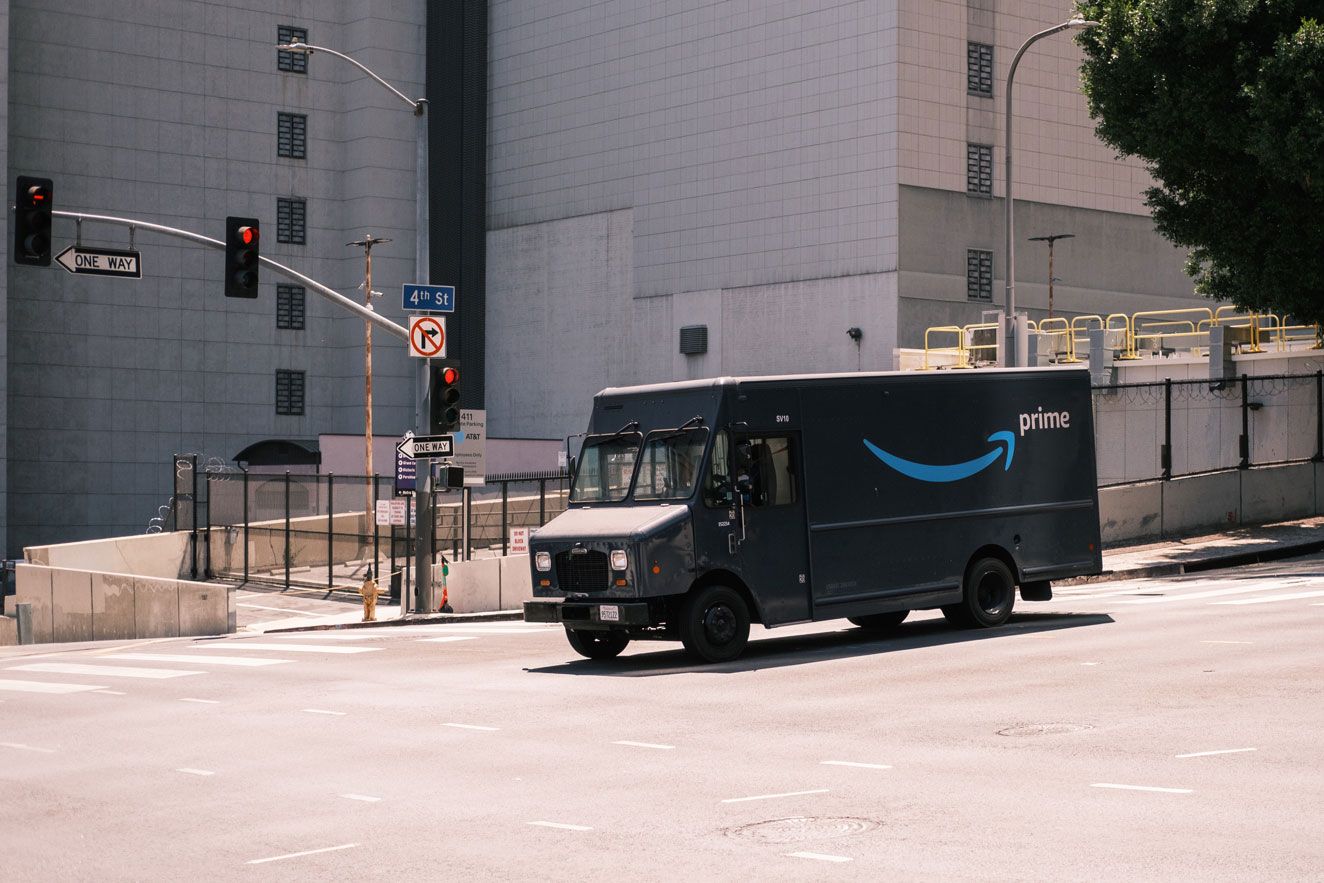
Vibration tests measure how your packages will fare during transport. It simulates the types of vibrations that packages may be subject to (e.g. on trucks or planes) which may cause cartons to come apart at the seams.
There are 2 common types of vibration tests:
- Random Vibration: This simulates a truck or plane ride.
- Sine Vibration: This identifies which frequencies are more damaging to your products.
Each packaging has a natural frequency, which is its natural vibration. A frequency sweep is performed by moving up and down from a low to a high frequency. During the frequency sweep, the package is placed on the vibration table.
When it reaches the natural frequency of the package, the table will become more still. This means the vibration and natural frequency match. When that happens, there are more chances of damage due to resonance. The goal is to have the vibration away from the package’s natural frequency.
The international standards for vibration testing are:
- ISTA 2A: Packaged-Products weighing 150 pound (68 kg) or Less
- ISTA 3A: Parcel Delivery System Shipments 150 lb (70kg) or Less
- ASTM D3580 - 95: Standard Test Methods for Vibration (Vertical Linear Motion) Test of Products.
FedEx’s ISTA-6-FedEx-A utilizes random vibration testing as well as rotary vibration testing:
5 - Packaging Moisture Level Test
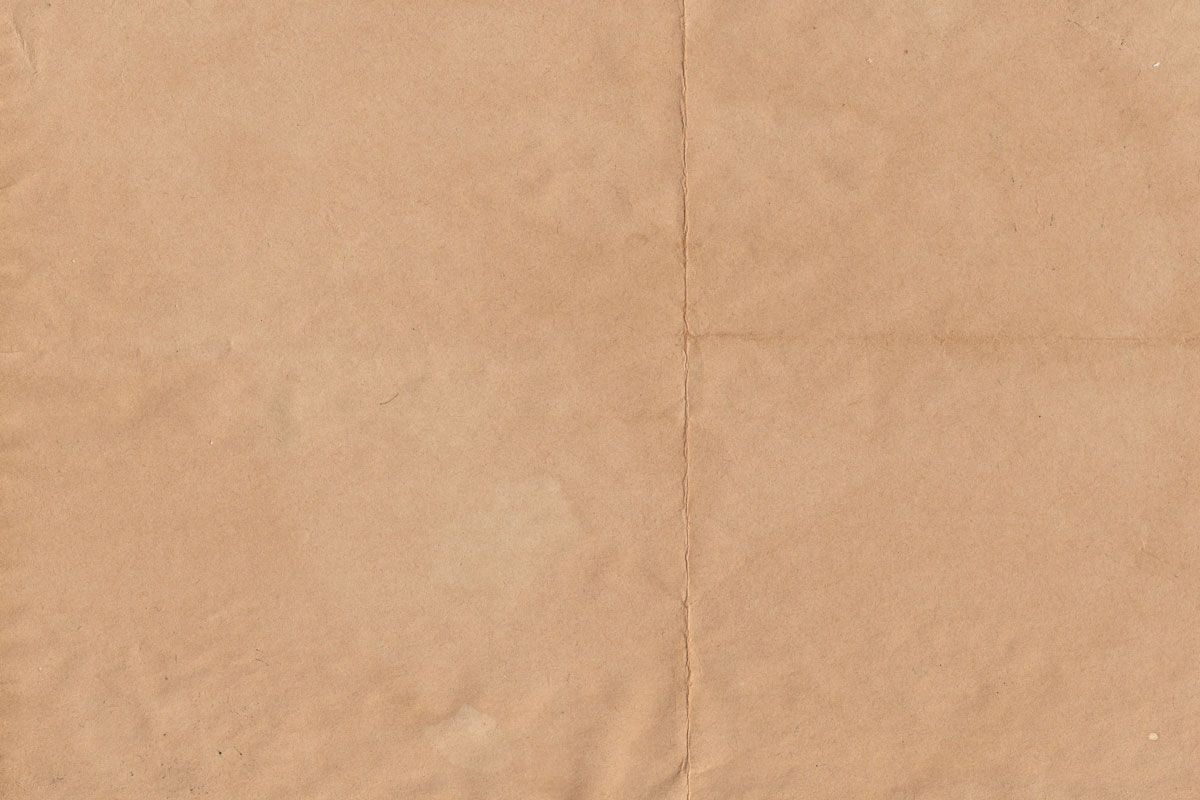
In our blog post about how weather affects packaging material, we talked about how high humidity levels in the environment lead to internal moisture within cardboard, and this has a direct impact on the strength of corrugated boxes such as mailer boxes or shipping cartons.
Some parts of the production process, including printing and gluing, all contain moisture. Coupled with high humidity levels in which your packaging boxes may be produced, this means that more time may need to be allocated to drying your packaging or corrugated boxes.
Because of this, one method of testing your packaging and how much moisture it contains is to use a moisture meter. A moisture meter measures the percentage of moisture in the material itself, and is an indication of whether your boxes need more time to dry.
As a rule of thumb, moisture levels should be no more than 25% (the lower, the better).
For packaging with high moisture levels, it may feel a bit flimsier, but this may not be an indication that your box is in fact weaker. For this, you can run the Mullen's test (burst tests) to truly test the strength of your packaging. If you do find that your boxes feel a bit flimsy, take them out of your shipping carton and give them some time to dry out!
--
About PackMojo
We make it easy for businesses to get affordable, high quality, custom packaging. Through our platform, you can get instant prices, order in low volume starting from just 100 boxes, and have your packaging orders delivered anywhere in the world. We work with a network of trusted and vetted suppliers across the world to manage this supply chain so that you can focus on growing your business.