E-commerce stores, small businesses, and even boutique brands are often faced with the challenge of reducing the cost of their packaging and shipping. You always want to get packaging materials that protect your products, perfectly showcase your brand, and provide an unforgettable unboxing experience. However, you are sometimes left with little budget to make all of it happen. With a pandemic underway, we see this problem intensifying. Several countries are going into lockdown and many economies are seeing a downturn. This is causing more and more businesses to face financial constraints.
But what if there was a way to get high-quality packaging and a killer unpacking experience without it being a burden on your budget?
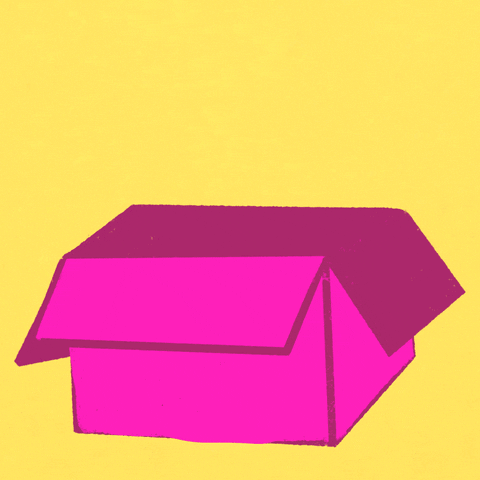
Here are 5 tips to help you optimize your packaging to reduce the cost of shipping from your suppliers to you.
1. Rethink the kind of boxes you use
The first thing you need to assess is your packaging. How are you packaging your products to be shipped and more importantly, what are you packing it in? As a general rule, it is best to keep your packaging compact and avoid excessive packaging materials like foam pellets and bubble wrap.
In terms of boxes, it would be beneficial to use boxes that can be flattened and shipped to you. Thereby allowing you to ship more boxes at an affordable price. Mailer boxes and folding cartons work best. Corrugated mailer boxes are naturally sturdy and the corrugation feature ensures your products are safe during delivery.
Additionally, mailer boxes and folding cartons can be customized with printing on the outside and inside of the box, giving you a chance to be creative with your design and your brand story. Your customers are also guaranteed to have an exciting unboxing experience.
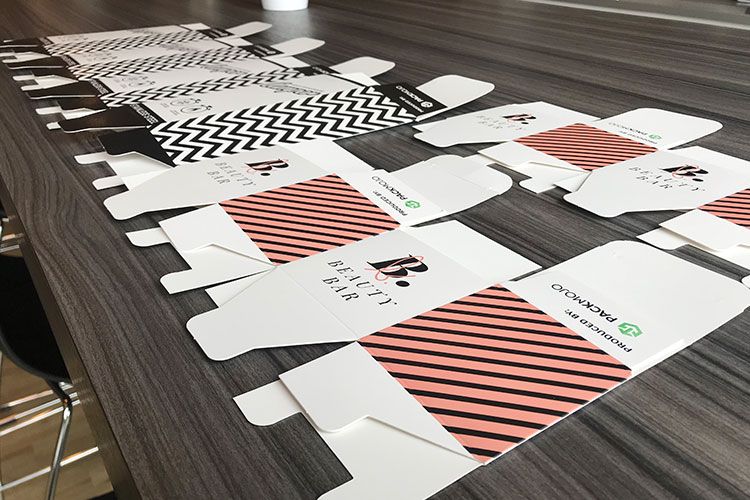
2. Optimize for weight and space occupied
The cost of packaging is also dependent on the weight of your packaging materials and the space they occupy. Particularly for air freight, the volume and space are usually capped at a certain limit. Shipping by ocean has always been cheap. However, in case you choose to ship via air, it is best to keep your packaging materials light (think folding carton boxes). This will not only save you some extra dollars but also makes the shipment a lot easier to handle. The more economical option is always to ship via ocean. However, there are certain restrictions on minimum weights while using ocean freight. In this, lighter shipments might make it harder to hit the minimum requirement. More on that in my next point.
3. Consider shipping via ocean
The cost of shipping via ocean is cheaper than air. When shipping by ocean, you are usually charged by the cubic meter (CBM). In other words, the space your packaging material is occupying. In comparison, there is less importance placed on the weight of each unit, which allows you to lower your costs. However, to be eligible to use ocean shipping, the total shipment size required is usually a minimum of 100kgs (220lbs). Even with this restriction, it can sometimes be cheaper to ship 100kg shipment than to use air freight to ship something lighter.
Here’s an example. I used PackMojo’s custom box quote tool to generate the following order:
- Mailer box - 4" x 4" x 3.75" - printing on the outside of the box
- 300 units (around 45kg) to be shipped to California from China
Because the total weight of these boxes is under the 100kg minimum, I won't be able to use ocean to ship my packaging. Instead, the options I have available are only by air, and the lowest cost for this is:
- US$615.50 to ship 300 units with a 13-16 day shipping time.
This brings the total cost to US$906.50 for 300 boxes, which is equal to US$3.02/box.
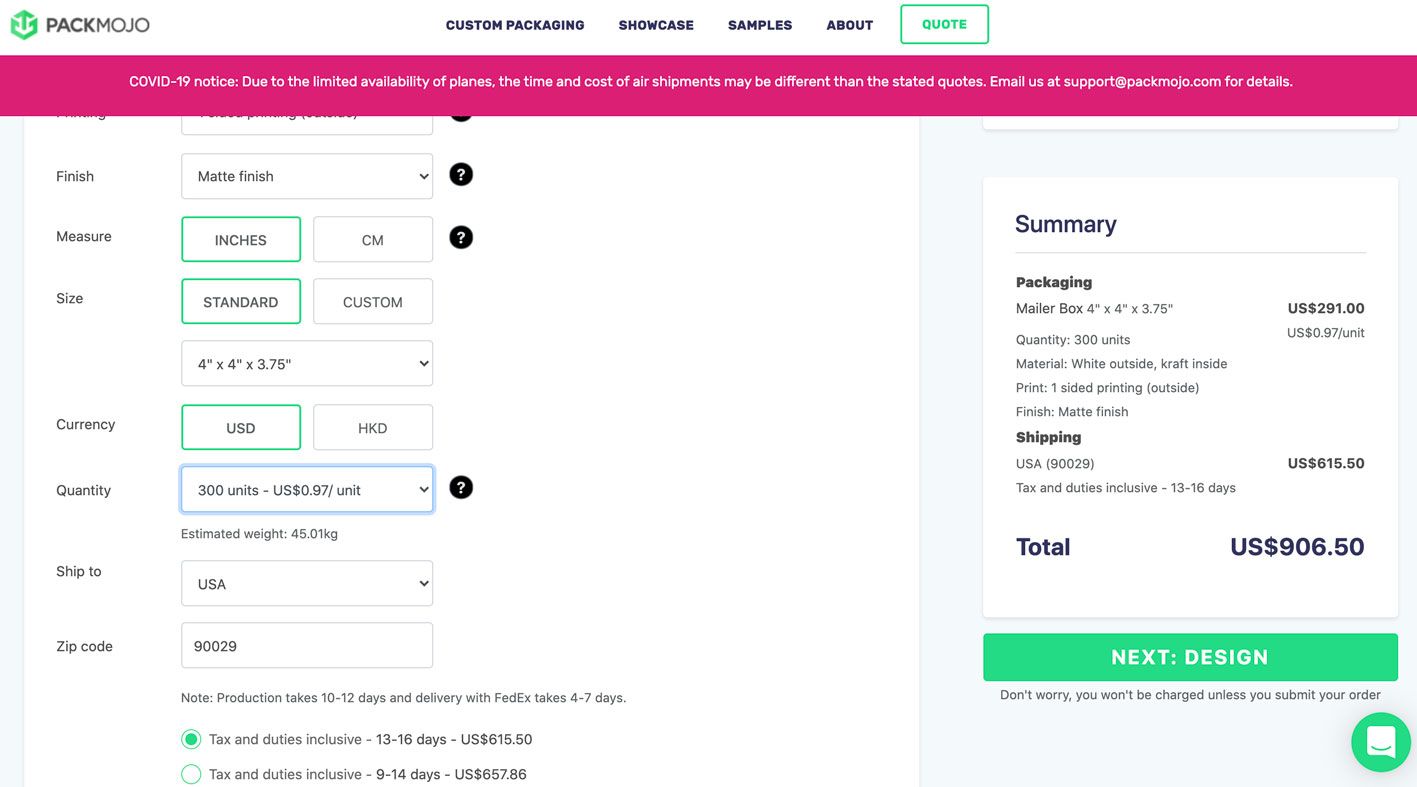
Now, let's say that I place the same order but for 1000 units instead (which equals around 148kg in total weight). In this case, I would be eligible for ocean shipping, and the lowest cost to ship by ocean is:
- US$271.57 to ship 1000 units with a 31-37 day shipping time.
This now brings the total cost to US$951.57 for 1000 boxes, which is only US$0.95/box! By spending only US$45.07 more, you can get 700 more boxes. If time is not a constraint, this alternative could result in significant savings.
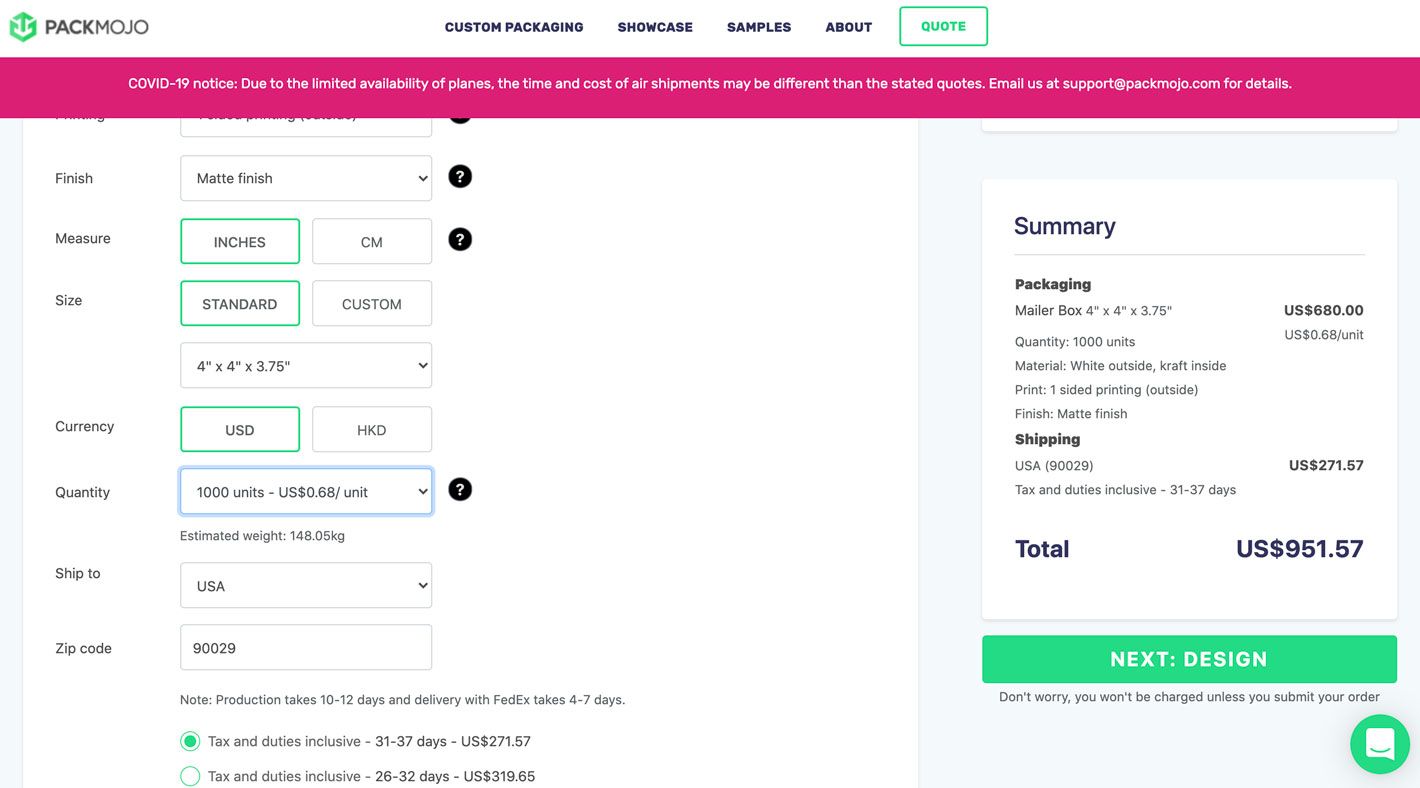
This comparison between air and ocean holds greater significance in the current pandemic situation. Due to the shortage of cargo planes, the price of air freight has increased around 4-5x the price of ocean freight on the same volume/weight of the shipment.
4. Start the process earlier than you normally would
Since ocean freight takes longer to ship, it is better to order in advance if you want to use this alternative and save costs. Ordering in large quantities has its own set of benefits. It is always better to have extra packaging materials to cater to a surge in orders during the holiday season or when you host a sale. It is also an effective way to ensure you have all the necessary materials to fulfill orders even during times of national emergency or a crisis. Your customers will appreciate the fact that you can continue to cater to them even in uncertain times.
Additionally, since mailer boxes and folding cartons can be flattened, it is easier to store them. You are likely to calculate lesser inventory costs for storing these types of boxes as opposed to rigid cartons, which cannot be flattened.
5. Make sure to evaluate your strategy regularly
If you are just starting off, you might be inclined to order smaller quantities and ship using air. But, as your company grows, it is imperative that you re-evaluate your packaging materials as well as your shipping methods. With air and ocean freight prices constantly fluctuating, always keep an eye on them and track your spendings to efficiently reduce costs wherever possible.
With these 5 tips in mind, you are bound to fully optimize your packaging to reduce costs while making sure your packaging makes the best impression on your customers.